|
|
Project
Summary: East Kelly Avenue Housing
OWNER/DEVELOPER
Jackson Hole Community Housing Trust
ARCHITECT
HandsOn Design
LANDSCAPE
ARCHITECT
Hershberger Design (designer formerly with Design Workshop)
CONTRACTORS
SMS Modular/ Two Oceans Builders
PROPERTY MANAGEMENT
Jackson Hole Community Housing Trust
FUNDERS:
|
TYPE:
|
The Jackson Hole Community
|
Private donations
|
Jackson State Bank
|
Construction Loan
|
First Interstate Bank
|
Construction Loan
|
DEVELOPMENT
TYPE:
Deed restricted for sale single family homes with 99 year
land lease.
RESIDENT
PROFILE:
Area working class residents, maximum of 120% AMI.
DENSITY: 23 units per acre
DEVELOPMENT
PROFILE
Type |
#/Units |
Size
(sf) |
Sale Price |
2
BR |
28 |
930 |
$155,000 on avg. |
Total |
28 |
|
|
Laundry: Each unit has laundry in the basement
Courtyard/play: Courtyard at each
site
Parking: 60 surface spaces
Total site area:
52,500sf (1.2 acres) |
CONSTRUCTION
TYPE
Modular units of OSB sheathing, 2x6 studs and open wood truss floors.
DEVELOPMENT
COSTS:
Land cost: $1,700,000; Constr. costs:
$6,500,000; Other costs: $550,000; Total
development costs: $8,750,000 ($312,500/unit);
Completed in phases over 2004.
|
|
|
East
Kelly Avenue- Jackson Town
Green Features
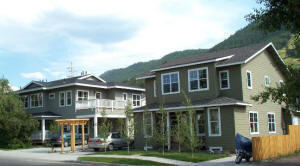
As in numerous
communities, housing costs in Jackson Hole, Wyoming are beyond the reach of many of the
area’s workforce. The Jackson Hole Community Housing Trust responds to this need by
subsidizing the development of deed restricted housing for the families and individuals who
contribute to and diversify their populace. The residents served by the Housing Trust would
not be able to remain a part of the community without projects such as the East Kelly Avenue
Housing which provides 28 affordable units.
The project is built on two
nearby sites on East Kelly Avenue in the heart of an established residential
neighborhood within the town of Jackson. Its vernacular celebrates the mixed
scale neighborhoods and development patterns historically found in mountain
towns of the Rocky Mountain West. One fourplex and four duplex units designed
to resemble larger single family homes are built on the site closer to the center
of town. On the same street towards the edge of town the units are single family
detached homes and duplexes. All the units are of modular construction.
Great care was taken to positively
impact community attitudes toward affordable housing, increased density and modular
construction - not only by drawing on the context of Jackson’s older housing stock
but also through intelligent and respectful site planning. Half the units face mid
block alleys, treating them as interior streetscapes in a gesture towards the future
development of Jackson. All units incorporate front porches and public mid block
walkways connecting street and alley to encourage walking, cycling and interaction
between residents and neighbors. Backyards are generously landscaped and treated as
unfenced courtyards.
The sites were selected primarily
because of their “in town” location, close to established businesses, public
transportation, and bicycle routes. The 270 project, called Arbor Place, replaced a
large parking lot and three accessory structures with 12 affordable homes. Existing
trees and plantings were preserved and incorporated into Arbor Place. The 565 project,
named 12 Pines, replaced a single home and rental trailer with 16 affordable homes
painstakingly inserted between several existing trees and accessible to a large public
park via the alley. The majority of units at 12 Pines are single-family detached homes
for families with children.
To make the project financially feasible
and provide the community with an example of urban density in excess of the town’s current
regulations but in line with Jackson’s “Town as Heart” initiative, a year long F.A.R. bonus
had to be enacted for all 100% deed restricted housing projects along with a reduction of
the parking spaces required. The project serves the community by setting a positive example
for future homeowners and developers of just how attractive and comfortable modestly sized
units can be, that density concentrations within established town boundaries are to be
embraced not avoided, and that modular construction techniques can result in high quality
projects indistinguishable from less efficient construction methodologies.
Modular construction
was used because of construction costs and staging constraints. This approach, along with the
repetitive nature of the unit layouts, allowed for a high level of quality control and early
troubleshooting of problems. These efficiencies allowed the specification of durable, low
maintenance finishes and period details such as laminate flooring, hardwood stair treads, deep
windowsills, period casing and handrails. Exterior finishes include fibercement siding and trim,
divided light vinyl windows, exposed rafter tails and split faced concrete block lightwell
enclosures.
The modular construction facility receives
building materials in bulk by rail, and is located approximately 120 miles from Jackson. By Wyoming
standards that’s local, reducing embodied energy. During fabrication, construction materials were
used to maximum efficiency and waste was recycled directly by the modular fabricator. Prefabricated
floor trusses used to accommodate clear spans and ductwork have the added benefit of using smaller
members harvested from younger trees. Painted MDF trim, laminate floor and cabinetry feature
particleboard substrates produced from sawmill waste products. At the job site, a separate dumpster for
wood products was maintained, and taken to the local recycling center. To encourage continued recycling,
each housing unit has a dedicated cabinet for small recycling bins in the kitchen and an enclosed exterior
storage compartment integrated into the rear porch for both recycling and trash stockpiling. To minimize
water waste, an automatic sprinkler system timed to minimize surface evaporation maintains the landscaping.
For improved Indoor Air
Quality (IAQ), the modular building components were stockpiled at the fabrication facility for
four months prior to delivery, giving construction materials time to offgas. To avoid moisture
issues that can contribute to IAQ problems, exterior walls were designed to minimize condensation
and to dry to the exterior. Features that make the envelope more energy efficient include double
glazed windows, insulated floor trusses to minimize ductwork heat loss and dropped ceilings at
bathrooms for an unbroken insulation layer above the exhaust ductwork. Forced air heat and domestic
hot water are delivered via a natural gas fired furnace and water heater. The Jackson Hole climate
does not require supplemental cooling.
Lessons Learned from the Architect:
Be sure to do your homework if you plan to suggest a technology or material people aren’t
familiar with. If you come to the table knowing what it will cost, where to get it and how it
benefits the project you’ll have a much greater chance of success.
Green Features
Click here to see the AIA Affordable Green Guidelines
|
East Kelly Avenue Housing
|
Compact Development |
The project density is 23 units per acre.
|
Daylighting |
Stairways and closets are located on party walls, allowing all other spaces to be on exterior walls with ample windows.
|
High Performance Windows |
High-performance double glazed vinyl windows. |
Energy Star Appliances/Lighting |
All units are equipped with Energy Star Appliances. |
Water Efficient Landscaping |
To minimize water waste, an automatic sprinkler system timed to minimize surface evaporation maintains the landscaping. |
Low VOC Materials |
The modular building components were stockpiled at the fabrication facility for four months prior to delivery, giving construction materials time to offgas. |
Other Innovations |
Modular construction was used for a high level of quality control, an;d cost and resource savings. During fabrication, construction materials were used to maximum efficiency and waste was recycled directly by the modular fabricator.
|
|