Process Failure
Risk Analysis (PFRA)-Disassembly Risk Failure Analysis (DRFA) as
part of TQM Improvement Practice
Author:
Margarita Rodriguez
Department:
Industrial &
Manufacturing Engineering
Professor:
Paul G. Ranky, PhD,
PMP
Course:
IE 673 -Total
Quality Management- Live
Email:
mr244@njit.edu
eLearning
Pack ID:
IE 673-Spring-2009-80-79
Table of
Contents:
Scope
& Purpose.
PAGEREF _Toc228443460 \h 3
Methodology.
PAGEREF _Toc228443461 \h 4
Seven key aspects of the PFRA..
PAGEREF _Toc228443462 \h 4
Rating.
PAGEREF _Toc228443463 \h 6
Collaborating Companies.
PAGEREF _Toc228443464 \h 8
TQM BASED QUESTIONS.
PAGEREF _Toc228443465 \h 8
Process Failure Risk Analysis
Modeling.
PAGEREF _Toc228443466 \h 8
Other things to consider.
PAGEREF _Toc228443467 \h 11
Reference.
PAGEREF _Toc228443468 \h 11
INTRODUCTION AND PROJECT
OBJECTIVE
Process-related Failure Risk
Analysis Method (PFRA) is a systematic, rule-based, quantitative
and open source computational method developed to identify
failure risks, and/or failure processes, which can include
disassembled sub-assemlies, objects and components. PFRA is a
part of the family of Failure Mode and Effect Analysis (FMEA),
“aimed at minimizing dissatisfaction and financial loss for
process related failure risks” and is applied usually during the
planning stages. (Ranky). It addresses negative quality and is
concerned with potential events that can make any process,
including service, or even a disassemble process fail. PFRA
helps to understand the problems then see the solutions, and
then apply the learned problem solving skills to other, new
challenges by understanding some of the following concerns among
others including:
 |
What could go wrong
with the product or the processes involved when
disassembling the product / or executing the process,
like assembling the product, or one or more of its
components? |
 |
How badly
might it go wrong, and what could the financial loss be?
|
 |
Which
are the highest risk processes / operations when working
on the product? |
 |
What needs to
be done to prevent failures? |
 |
What tools
and fixtures are required to prevent failures, and
reduce the risk? |
 |
What
education is needed for line management and operators to
reduce, or prevent failures? |
The
purpose of this project is developing and delivering clean
renewable energy to homes and business in collaboration with
Cattron, Stanley Vidmar, Bolaball and
I.D. Systems, INC. Bio-Green
Alternative Energy Solutions is intended
to replace fuel sources without the undesired consequences of
the fuels. Our
company’s mission is bringing innovative ways to cover the need
to overcome the shortage in energy by developing secure energy
solutions that are sustainable and are technologically and
financially viable.
Our
experience in industry gives us a deep insight into the
technical, policy, economic, and regulatory challenges being
faced by our energy clients. We help clients view energy issues
in a broader context, and to manage energy strategically to
ensure that their clean energy and energy reduction solutions
grow with the organization.
The objective of this
assignment is to introduce Process Failure Risk Analysis (PFRA)
method and software tool, in the TQM context, with real-world
and R&D challenges, and cases. Our company Bio-Green
Alternative Energy Solutions along
with our four collaborating companies will use the PFRA model to
identify failure risks and processes that may occur with the
Recycle Process and
avoid potential product/process/service failures as early as
possible in order to
reach OUR TQM objective.
Bio-Green Alternative Energy Solutions implements
the Process Failure Risk Analysis Method’ (PFRA)
as a Total Quality Management method to assess the risk involved
in different processes of our project with the help of provided
case studies.
There are seven key aspects of
our generic methodology that we as a company respect and follow,
before beginning to work on any process failure risk study with
our PFRA Tool :
-
Define scope, function
and purpose
Includes the definition of the
system or sub-system, or any product, or process design that
needs to analysis
-
Identify potential
risks and failure modes, and their effects
When applying the PFRA
technique during the process, and creating, or analyzing the
existing BOM, the team should be able to gradually deepen the
product, process or system design analysis and locate all
potential failures at the earliest possible stage.
-
Prioritize potential
failures
All faults should be ranked
and critical quality, or cost, or safety related faults should
be located and eliminated by the cross-functional team as early
as possible. The key is to make sure that the design and
manufacturing and other processes include verification controls
which can identify potential failures.
-
Select and manage
subsequent actions
If the risk of potential
failures is high, following our basic TQM principles, an
immediate control plan must be devised and subsequent actions
should be taken to control the situation. By employing
prevention-oriented system warnings, by means of
sensory-processing systems and statistical analysis methods,
risks can be minimized, by designing TQM into the product,
process or service.
-
Observe and learn
For each system or product
design, PFRA represents a dynamic, living knowledge-managed
document that needs to be kept up-to-date. It should not be
retrospective, but kept as a valuable source of information for
current and future products.
-
Document the process
Store the PFRA contained
information in a widely accessible format. Enter the values into
the PFRA spreadsheet on a relative scale, determined by the
local PFRA Team, as well as by the local customized standards
they follow.
-
Entering the values
into PFRA spreadsheet
Within this analysis this are
three main values that will be used Severity (a rating of the
severity or seriousness of each potential failure effect),
Detection (a rating of the likelihood of detecting the failure
cause) and occurrences (a rating of the occurrence likelihood
for each potential failure cause). These values in return will
help to calculate the RPN (Risk Priority Number).
Severity is a rating
corresponding to the seriousness of the effect of a potential
failure mode and range from 1 to 10, with 10 being the most
severe. The reason behind applying severity is to quantify the
seriousness of failing. The values are shown below:
Rating = 1 No Effect on the part/ component, and/or on
system performance, and/or on subsequent process, or operation.
Default Value
Rating = 2: A Very Slight Effect on the part/ component,
and/or on system performance. Customer probably won’t notice
this.
Rating = 3: A Slight Effect on performance, or process
operation. The customer is slightly disappointed, but no vital
fault will be noticed.
Rating = 4: A Minor Effect on performance, or process
operation. The customer will notice a slight deterioration but
no vital fault will be noticed.
Rating = 5: A Moderate Effect on performance, or process
operation. The customer is disappointed, and no vital fault will
be noticed.
Rating = 6: A Significant Effect on performance, or
process operation. The customer is significantly disappointed,
and a fault will be noticed that may cause part repair, or
rework.
Rating = 7: A Major Effect on performance, or process
operation. The customer is severely affected, but system is safe
and operable. Fault is obvious and will cause part replacement.
Rating = 8: An Extreme Effect on performance, or process
operation. The device fails to start, or operate. The customer
is severely affected, system is not operable but is safe and the
fault will be obvious
Rating = 9: A Very Serious, Potentially Hazardous Effect
on performance, or process operation. The customer is severely
affected; system is not operable, potentially unsafe and the
fault is obvious.
Rating = 10: A Hazardous/ Dangerous Effect on
performance, or process operation. The customer is severely
affected; system is not operable and unsafe. The fault is
obvious, not complying to government regulations, and is
hazardous and or dangerous.
Severity is used to calculate RPN or Risk Priority number. When
analyzing RPN, the highest value is analyzed first, trace the
cause and then eliminate it. Once completed the same process
should be applies to the medium and then the lower values.
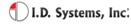
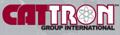
The
following are some of the TQM questions by
Bio-Green Alternative Energy
Solutions PFRA
team and along with our four collaborating companies we come up
with the answers as follows:
Question #1:
How can we
minimize damage to the foundation of the wind turbines?
Answer: By
installing Vibration monitors and the fluid contamination
monitors. Vibration monitoring is used to detect faults in the
bearings and gearing. There are two categories: First category
uses sensors mounted to the bearing housing or gear case to
detect characteristic vibration signatures for each component.
The signature for each gear mesh or rolling-element bearing is
unique and depends on the geometry, load, and speed of the
components. The monitoring system then compares the signature
during operation with the characteristic signature and flags any
anomalies. The second category includes the ‘shock-pulse’ or
acoustic systems that use high-frequency, narrow-band vibration
sensors to detect structure-borne pulses that occur when a
rolling contact or gear mesh encounters a discontinuity in the
surface, indicative of wear or debris particles.
Question #2: What
type of analysis was made to determine the level of online
contamination?
Answer:
by implementing On-line contamination monitoring technology
which takes several forms. One system type applies a magnetic
field to a contained fluid stream to detect the presence of
“Ferro-magnetic debris”, which is indicative of wear particles
from rolling or rubbing contacts. Another type is originally
develop for evaluating the cleanliness of fluids used in process
industries, and which can be adapted to hydraulic and lubricant
fluids. These systems use a laser light source and target
arrangement to count the particles, seen as obstructions, in a
fluid stream.
Question #3:
Is training critical for quality and maintenance?
Answer:
A thorough personnel training is essential for proper
maintenance and for effective fault and failure diagnosis. Most
turbine manufacturers offer comprehensive training for their own
technicians, as well for the site owner’s personnel.
Question #4: Does
the size, shape, and weight of the sensor affects the vibration
monitoring system?
Answer: It is hard
to really understand the factors that
affect
performance, reliability. However, just the size can affect it,
so we must chose a reliable and light weight sensor.
Question #5: How to
reduce Maintenance Cost?
Answer:
Develop Logistics
Plan: A comprehensive logistics plan allows
to efficiently deal
with breakdown
problems when they occur and
minimize turbine downtime. At a minimum, a logistics plan
will identify major
failure events and list the tasks required for affecting a
repair. A thorough plan will
anticipate likely failures and prepare a spares inventory,
manpower, and equipment.
Question # 6:
How the development of a Component Reliability Model can
determine System reliability?
Answer:
A statistical reliability model of the major turbine components
would be a useful planning tool for wind farm maintenance,
assisting staff to budget spares, manpower, and equipment for
the project’s life. From a development point of view, a
reliability model will identify the risks associated with
component types, allowing planners to steer their equipment
selection process toward lower-risk configurations. Trending the
reliability data over time can validate the effectiveness of
preventive maintenance strategies to improve component
reliability.
Question # 7: What
does failure represents?
Answer:
Determine the Root Cause. Although the
Bio-Green
Alternative Energy Solutions
as a
wind plant
operator is primarily interested in replacing a failed component
and getting our machine back on-line, a failure always
represents an opportunity for improvement, and an included
failure analysis is an essential part of our continuous quality
improvement process. Evaluating the root cause of a major
component failure is essential to determining if the failure is
due to manufacturing quality, product misapplication, design
error, or inappropriate design assumptions.
Question # 8:
Why considering Re-Evaluating Design Standards?
Answer:
The large number of load-carrying component failures has led to
concerns about the applicability of the standards that are used
for component design. Existing standards and design methods
should be reviewed in light of experience to determine if the
loading and response assumptions are justified and if the
assumed operating conditions accurately reflect the wind turbine
operating environment.
Question # 9: How
to calculate the Cost
of Energy for a wind turbine system?
Answer: By using
the following Formula:
COE= [
ICC FCR LRC / AEPNET ] + Bio-ALTES
COE Cost of Energy ($/kWh)
ICC Initial Capital Cost ($)
FCR Fixed Charge Rate
(%/year)
LRC Levelized Replacement
Cost ($/year)
Bio-ALTES’s Operations and
Maintenance Costs ($/kWh)
AEP Annual Energy Production
(kWh/year)
Question # 10: How
does elevation affects performance of Turbines?
Answer:
Wind speed increase
substantially with higher elevations. Higher locations have a
greater potential wind resource. Higher elevations also help
minimize the height of the wind towers.
Question # 11: Is
access to Transmission
Line Adequate?
Answer: Bio-ALTES must install
new, overhead distribution lines at the site, or that the
existing overhead electric line is capable of handling the new
electric load without major modifications.
Question # 12:
What are the Impacts of Wind Power Generation to the
environment?
Answer:
Significant tree clearance, line construction, and access would
be required for other potential sites that are not in the
“vicinity” of existing distribution lines.
This means tree
deforestation which affects wild life. A solution will be
installing the turbine in the open sea instead of land fields.
 |
Noise
Study, Photo Simulation, Shadow Analysis, and Wind Data
Analysis
|
 |
Preliminary Acoustic
Noise Impact Assessment
|
 |
Wind Resource
Evaluation
|
 |
Bird Risk Study
|
 |
Notice of Intent for
Storm Water Discharges
|
 |
Building Permit
|
 |
Land Use Before and
After Construction |
 |
Trail Access during
Construction |
 |
Construction
Insurance |
Download PFRA Spreadsheet for Bio-ALTES
SUMMARY
In this project we used the TQM concepts we have learned up
until this point to analyze one companies that were
featured in our case studies and then discussed how we could
apply the methods to improve one of the
companies. We were also introduced to the PFRA method of
analyzing potential failure modes and performed
this analysis on one of the companies.
Customers demand high quality, reliable products. However, the
increasing complexity of products has
significantly increased the costs associated with testing to
assure quality and reliability. Testing is typically done
in the late stages of development, but this is inefficient and
wasteful. The challenge is to design in quality and
reliability early in the development cycle, and therefore
eliminate the need for extensive testing and redesign
costs.
PFRA is a methodology for analyzing potential reliability
problems early in the development cycle where it is
easier to take actions to overcome these issues, thereby
enhancing reliability through design. PFRA is used to
identify potential failure modes, determine their effect on the
operation of the product, and identify actions to
mitigate the failures. A crucial step is anticipating what might
go wrong with a product. The early and consistent
use of PFRAs in the design process allows the engineer to design
out failures and produce reliable and safe
products that meet or exceed customer expectations.
Further Work Needed
We could continue to research and investigate potential failures
through simulations and methods at
Bio-Green
Alternative Energy Solutions.
Research is now being done to increase the knowledge of wind
resources. This involves the testing of more and more areas for
the possibility of placing wind farms where the wind is reliable
and strong. Plans are in effect to increase the life span of the
machine from five years to 20 to 30 years, improve the
efficiency of the blades, provide better controls, develop drive
trains that last longer, and allow for better surge protection
and grounding.
Templates Used
PRFA Excel Templance by Paul
Ranky
MS Excel 2003
Reference
Ranky, P.G.: An Object
Oriented System Analysis and Design Method (CIMpgr),
Published by ADAM at http://www.cimwareukandusa.com, © Copyright
by CIMware Ltd. UK and
CIMware USA, Inc.
Ranky, P.G.: A Case-based Introduction to Total Quality
Management and the International
Quality Standards,
Published by ADAM at http://www.cimwareukandusa.com, © Copyright
by CIMware Ltd. UK and
CIMware USA, Inc.
http://www.madehow.com/Volume-1/Wind-Turbine.html
|